Stop Wasting Time! Speed Up Your Precision Manufacturing Quality Checks
image for illustrative purpose
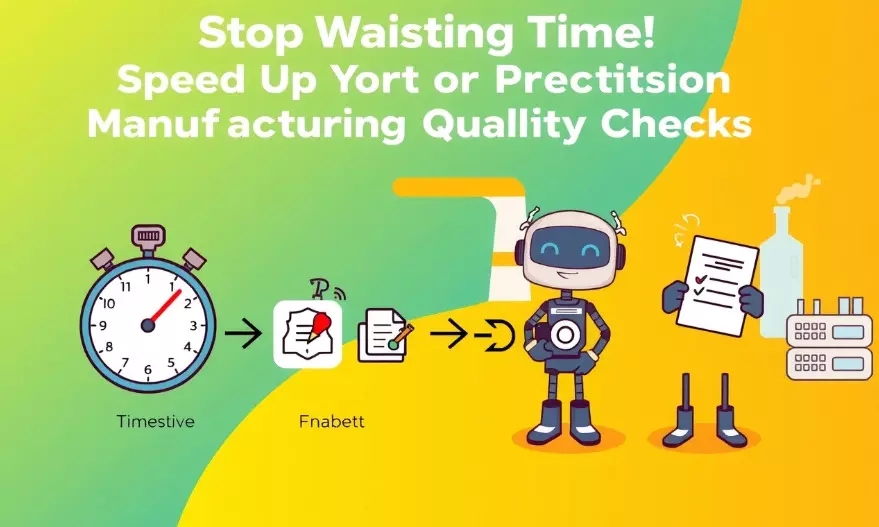
Have you ever wondered why your precision manufacturing quality checks seem to fall short? Many companies track defect rates and rework costs, but are these metrics genuinely reflecting the effectiveness of your current solutions? Surprisingly, a significant number of manufacturers overlook customer complaints and inspection times—key indicators that could reveal deeper inefficiencies. This isn't just a minor oversight; it could be costing you more than you realize. Ready to uncover what’s really going on? Let’s dive deeper…
The vice president of operations at a mid-sized aerospace supplier leaned over the inspection report, his knuckles whitening around the edge of the desk. "We doubled the QC team last quarter," he muttered to the quality manager. "How are defect rates still climbing?" The room fell silent—their "tried-and-true" approach of manual inspections and Excel tracking had backfired spectacularly. Technicians were drowning in paperwork, critical dimensions got missed in the 200-step checklists, and late shipments piled up. "Maybe adding more eyes wasn’t the answer," the quality manager admitted, tossing a mislabeled titanium bracket onto the table. Somewhere between overtime costs and angry client calls, they’d crossed a line—but quitting wasn’t an option. The board meeting was in 72 hours, and nobody had a solution.
The breaking point came at 2:37 AM on a Tuesday. Third-shift supervisor Maria slammed the emergency stop button when a misdrilled fuel nozzle jammed the conveyor—the fifth defect in two hours. Upstairs, the quality team was still manually cross-referencing spreadsheets from the *previous* shift. "We’re not just slow, we’re *wrong*," the VP realized, watching engineers argue over conflicting tolerance notes. Meanwhile, the CFO’s email pinged—a key client had quietly awarded their next contract to a German rival using AI-powered inspection. The boardroom whiteboard now read "72 HOURS" in red marker, half-erased like a countdown no one wanted to acknowledge. Someone muttered, "What if we’ve been solving the wrong problem all along?" The silence that followed wasn’t just tense—it was the kind where you could hear the coffee machine drip like a ticking clock.
Appreciate the case study example: www.kantti.net/jp/article-list
**"Wait—How Do You Even Define 'Quality' in Precision Manufacturing?"**
Let’s cut to the chase: Quality checks aren’t just about "looking good" or "working fine." They’re a science. 🔬 Ever wondered why some factories churn out flawless parts while others drown in rework? It often boils down to *measuring the right things*—like defect rates (think: "How many parts get tossed per 100 units?"). But here’s the kicker: Even a 1% defect rate can cost thousands if you’re making aerospace components.
**"But What’s ‘Close Enough’ in High-Stakes Manufacturing?"** 🤔
Tolerance levels are where things get spicy. A hair’s breadth (sometimes literally 0.001mm) can make or break a medical device. For example, if your CNC machine’s tolerance is ±0.005mm but your design specs demand ±0.002mm, you’re already playing with fire. Pro tip: Always cross-check tool calibration *before* the batch runs—not after.
**"How Often Should We Inspect? (Spoiler: ‘Whenever’ Isn’t an Answer)"**
I’ve seen teams inspect "when they have time." Big mistake. 🚨 Frequency matters:
- **High-volume runs?** Sample every 50 units.
- **Critical components?** 100% inspection + automated scans.
Fun fact: One automotive supplier reduced recalls by 30% just by switching from weekly to real-time laser checks.
**"Paperwork? Really?"**
Yep, and it’s not just bureaucracy. Traceability saves your bacon when a client asks, *"Why did batch #X fail?"* ISO 9001 isn’t a suggestion—it’s your paper trail lifeline.
💡 **Here’s the real question:** Are you measuring *enough*—or just *going through the motions*? (Hint: Your bottom line knows the answer.)
When it comes to speeding up precision manufacturing quality checks, root cause analysis often takes center stage. Some experts argue that focusing solely on defect rates or equipment performance metrics can overlook the subtleties of production process variability. Sure, tools like Fishbone Diagrams and the 5 Whys technique seem effective, but do they really address all underlying issues? What about human factors such as employee training and adherence to SOPs? While many tout these methods as future-proof solutions, others raise concerns about their applicability in diverse scenarios. If we continue down this path of rigid methodologies, how will we adapt to new challenges that emerge in quality control? It’s a thought-provoking dilemma worth considering.
To speed up your precision manufacturing quality checks without sacrificing accuracy, let’s dive into some practical steps that can make a real difference.
First off, consider automating repetitive tasks. For instance, using advanced vision systems can slash your inspection cycle time by up to 30%. Imagine how much more you could accomplish with those extra minutes! 💡 A tip here: ensure your vision systems are well-calibrated to maintain precision while speeding things up.
Next, set clear tolerance thresholds for critical dimensions—think ±0.001". This balance allows you to streamline inspections without letting defects slip through the cracks. Now, instead of 100% inspection, try statistical sampling; many companies find AQL levels like 1.0% effective for minor defects.
Don’t forget about training! Equip your team with rapid measurement techniques so they can align fixtures in under a minute. This little investment pays off big time!
Finally, keep an eye on metrics such as First-Pass Yield (FPY) and Defects per Million (DPM). If these numbers aren’t improving after implementing these strategies, it might be time to explore deeper challenges in your process.
By following these actionable insights, you'll not only enhance efficiency but also uphold the standard of excellence in your manufacturing operations!