The next big green thing: Steel
Policymakers worldwide focus a lot on reducing emissions from cars, planes and power plants. But they will succeed in getting to net zero emissions only if they also pay attention to less glamorous questions, such as how to modify the way we make steel
image for illustrative purpose
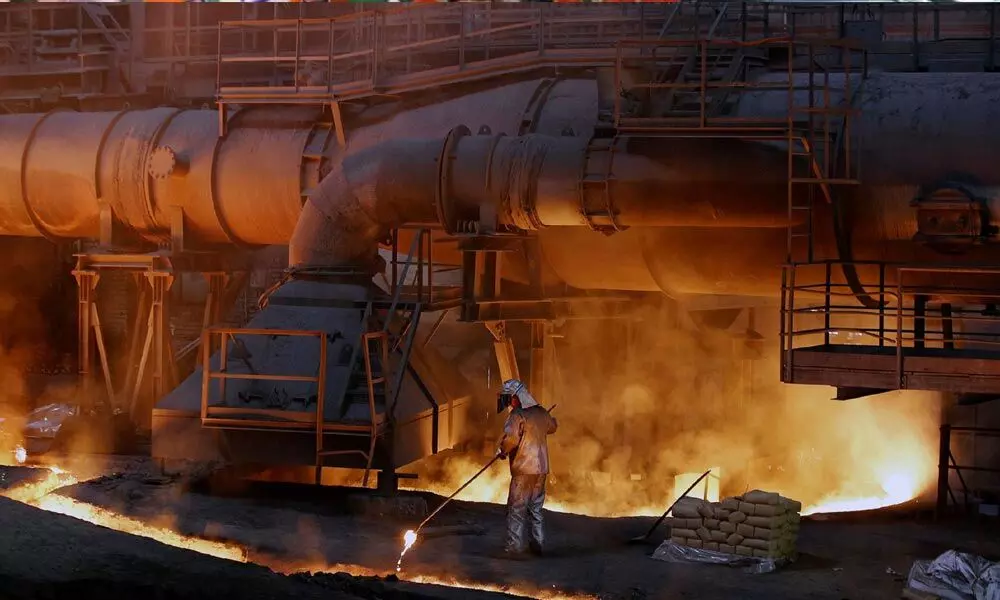
Steel production accounts for 7 - 10% of total carbon emissions
If you had to guess, which would you say contributes more to carbon emissions, air travel or steel production? If you guessed the Wright brothers' invention instead of Henry Bessemer's, you're wrong.
Steel production accounts for about 7 per cent to 10 per cent of total carbon emissions - twice what comes from air travel. Leading companies are now experimenting with new techniques to reduce these emissions, but it isn't easy. Indeed it demonstrates why bending the carbon curve is so hard. Decarbonising steel production requires a mix of new technology, regulatory and price changes, and business innovation - so it is a microcosm of the broader challenge facing governments and corporations as they seek to make progress on climate protection.
Steel is a core piece of the modern economy because it is strong, versatile and long-lasting. The process of making it, however, involves carbon emissions at multiple stages. The biggest is the reduction process, in which oxygen is removed from natural iron ore to form a purified pig iron, which is then combined with other elements to make steel. The oxygen is stripped from the ore by mixing it with coke, a form of coal, and the chemical reaction emits carbon dioxide. The mixture also must occur at very high temperatures, so it requires substantial energy, which typically involves more carbon emissions.
Alternative approaches to making steel - so-called green steel - are possible, but they're more expensive. As Bill Gates writes in his new climate book, "Why do we do it this way? Because it's cheap, and until we started worrying about climate change, we had no incentive to do it any other way." Gates estimates the extra cost in making green steel at 16 per cent to 29 per cent - a material but not astronomical premium.
The question thus becomes how rapidly the market share of green steel can expand over time. The stakes for both companies and the planet are high. The International Energy Agency projects that between now and 2050, global demand for steel will rise by a third. McKinsey estimates, however, that global steel companies will lose 14 per cent of their value, on average, if they aren't able to reduce their environmental impact. The consulting firm concludes that "decarbonisation should be a top priority for remaining economically competitive and retaining the industry's license to operate."
Leading steel makers are taking three basic approaches to create green steel. One is to reduce the carbon footprint of the blast furnaces used to smelt iron, for example by using biomass products rather than coke to remove the oxygen from the iron ore, or by capturing the carbon dioxide released from using coke. Such steps can meaningfully reduce emissions, but blast furnace changes alone can't achieve net zero emissions in steel production.
The second approach is to use electric arc furnaces to refashion steel scrap into new steel products. If renewable energy is used to power the furnaces, the result can be dramatically lower emissions. The challenges are to obtain sufficient supplies of renewable energy (and be able to store it) and of scrap steel.
The final route is to use hydrogen to transform the iron ore and also to power electric arc furnaces. When hydrogen is used instead of coke to remove the oxygen from iron ore, the byproduct is water rather than carbon dioxide. And when hydrogen is produced using renewable sources, it can be a steady source of green energy. This technology is available today, but it's very expensive.
Policymakers worldwide focus a lot on reducing emissions from cars, planes and power plants. But they will succeed in getting to net zero emissions only if they also pay attention to less glamorous questions, such as how to modify the way we make steel.
Although most of the work involved needs to occur in the private sector, governments can help. The role of hydrogen in particular cuts across many climate topics, not only the future of steel. Moving to hydrogen on a large scale across multiple sectors will probably require significant government assistance, given the research and development still needed, the scale of the investments, and the need to make sure emissions regulations - perhaps including carbon pricing - facilitate the shift.
As we approach the Glasgow climate conference later this year, the steel example illustrates a fundamental truth: Getting to net zero carbon emissions will require not just political will but also new technologies, many of which involve hydrogen. (Bloomberg)