What Is The Minimum Bottle Size For Series Accumulation Tables
image for illustrative purpose
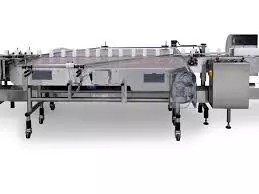
When designing a production line with accumulation tables, getting the bottle size right is crucial for ensuring smooth operations and preventing costly bottlenecks. What is the minimum bottle size for series accumulation tables?
The minimum bottle size for series accumulation tables is 1.0 inches (25.4mm) in diameter, according to industry standards and equipment manufacturer specifications.
While this is the technical minimum, it's essential to continue reading because the practical minimum bottle size often needs to be larger depending on your specific application, line speed, and product characteristics. Understanding these factors can help you avoid expensive mistakes in your line design.
Factors That Determine Your Actual Minimum Bottle Size
While 1.0 inches represents the absolute minimum bottle diameter, several factors influence your practical minimum size. Line speed is crucial - faster speeds require larger minimum diameters to maintain stability. Product characteristics like weight distribution and center of gravity also play a role. Additionally, the material of your bottles matters, as glass typically requires larger minimums than plastic due to its weight and fragility.
The shape of your bottles is another critical factor. Bottles with unusual shapes or those significantly taller than they are wide may require larger minimum diameters to prevent tipping, even if their base measurement meets the minimum requirement.
How Does Line Speed Affect Minimum Bottle Size Requirements?
The minimum bottle size requirements must be adjusted upward as production speeds increase. At speeds below 100 bottles per minute, you can often work closer to the minimum 1.0-inch diameter. However, at speeds between 100-300 bottles per minute, it's recommended to use bottles at least 1.5 inches in diameter. For high-speed lines running above 300 bottles per minute, minimum diameters of 2.0 inches or greater are often necessary to maintain stability and prevent jams.
What Are The Common Pitfalls Of Using Minimum-Sized Bottles?
Using bottles too close to the minimum size can lead to several operational issues. First, you may experience frequent line stoppages due to bottles tipping over or becoming misaligned. Second, the accumulation efficiency can be compromised, as smaller bottles are more prone to rotation and misalignment during accumulation. Finally, minimum-sized bottles often require frequent maintenance adjustments to guide rails and transfer points, increasing operational costs and reducing overall line efficiency.
To avoid these issues, many manufacturers use 25-50% larger bottles than the minimum required size, finding that the improved operational stability justifies any additional material costs.
How Do Different Accumulation Table Surfaces Impact Minimum Bottle Size?
The type of accumulation table surface significantly affects how small your bottles can be while maintaining stability. Stainless steel surfaces typically require larger minimum bottle sizes due to reduced friction. Tables with low-friction materials like UHMW (Ultra-High-Molecular-Weight polyethylene) can sometimes accommodate bottles closer to the minimum size, but they may require slower speeds. Specialized surfaces with rollers or conveyor belts might allow for slightly smaller bottles but often come with their own maintenance considerations.
The condition and cleanliness of the table surface also play a crucial role. Worn or dirty surfaces can increase friction unpredictably, making it harder to maintain consistent bottle movement and potentially requiring larger minimum bottle sizes to compensate for these variables.
What Alternatives Exist For Products Requiring Smaller Bottles?
Several alternative solutions exist if your product requires bottles smaller than the recommended minimum size for traditional accumulation tables. Single-lane servo-driven conveyors can handle smaller bottles more effectively, though they typically operate at lower speeds. Specialized handling systems with bottle pucks or carriers can also accommodate smaller containers by effectively increasing their footprint on the conveyor.
Another option is to use alternative packaging formats altogether. For instance, multi-pack configurations can create a larger combined footprint that works better with standard accumulation systems. Some manufacturers also opt for custom accumulation table designs with modified guide rails and contact surfaces engineered explicitly for smaller containers, though this usually involves higher initial investment costs.
Moving Forward With Your Accumulation Table Design
Before finalizing your production line specifications, consult with equipment manufacturers about your specific bottle dimensions and line speed requirements. This conversation ensures you're not only meeting minimum size requirements but also optimizing your line for maximum efficiency and minimal disruptions.