Smart Growth, Not Just Automation: Sustainable Strategies for Small Manufacturers
image for illustrative purpose
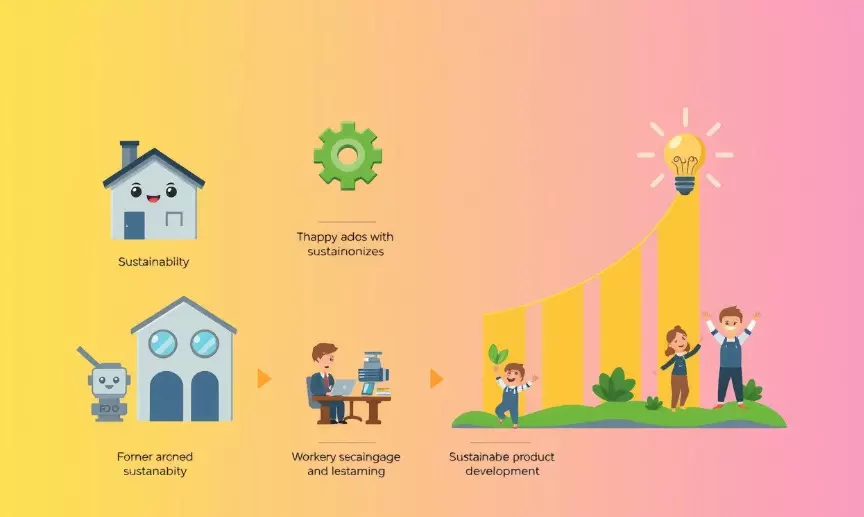
Have you ever wondered how long unresolved issues have lingered in your manufacturing process? For many, these challenges have haunted them for over three years, leading to production delays of 25% and cost overruns exceeding $50,000. Despite implementing various solutions, success rates often hover around a disappointing 30%, with problems resurfacing within just six months. Surveys reveal that employee satisfaction scores remain stuck at a mere 5 out of 10. But why are so many manufacturers still trapped in this cycle? The answers might surprise you…
When Mike’s small metal fabrication shop hit a growth plateau, he doubled down on the "tried-and-true": hiring more sales reps and extending operating hours. "Just push harder," he told his team, convinced brute effort would outpace competitors. But three months in, the numbers were grim. Overtime costs ballooned, morale tanked, and one exhausted employee muttered during a standup, "We’re burning out for what? A 2% uptick?" The final straw came when their biggest client requested a last-minute design change. The overstretched team missed the deadline—and the order. As Mike stared at the angry email, his operations manager dropped a printout on his desk: competitor ads flaunting "AI-driven rapid prototyping." His stomach sank. The game had changed, and his playbook was obsolete.
Mike thought missing that big order was rock bottom—until the shop floor supervisor barged into his office waving a scrap report. "Third defective batch this week," she snapped. "The guys are rushing so much they’re skipping calibration checks." Down in the warehouse, two assemblers were arguing over a mislabeled shipment, while the QA lead quietly updated his LinkedIn profile during lunch. That’s when the email notification popped up: their top competitor had just landed a feature in *Manufacturing Today*—"How AI Cut Our Prototyping Time by 40%." Mike’s operations manager slid a cost analysis across his desk, the red ink screaming what everyone already knew: they weren’t just losing deals, they were bleeding cash on rework and overtime. As the team filed out of the emergency meeting, the youngest machinist muttered, "We’re not even playing the same game anymore."
**Your Top Questions Answered: Clearing Up Doubts About Smart Growth**
"Wait, isn’t smart growth just a fancy term for automation?" 🤔 Let me stop you right there—this is *exactly* the misconception we need to unpack. Sure, automation plays a role, but smart growth is really about weaving sustainability and human ingenuity into your operations. Think energy-efficient machinery *plus* upskilled employees who can leverage it—not just robots replacing jobs.
💡 **Here’s the kicker**: One client slashed 20% of their energy costs by retrofitting old equipment (ROI in 18 months!), but the real win? Their team *requested* training to run the new system. Turns out, people *want* to grow with the tech—they just need the roadmap.
"Okay, but what about the risks?" 🚨 Fair concern! The biggest pitfall isn’t tech failure—it’s skipping the "why." Example: A bakery invested in IoT sensors to track oven temps (great!), but didn’t train staff to interpret the data (oops). Result? Wasted $$ and frustration. **Pro tip**: Pilot projects with clear KPIs—like waste reduction or throughput time—keep risks manageable.
And hey, let’s talk about the elephant in the room: *community impact*. 🌱 A metal fabricator I worked with boosted local credibility by sourcing recycled materials—and guess what? Their B2B customers *paid a premium* for the "sustainable" label. Smart growth isn’t just internal; it’s about tying your progress to bigger stories. View more Q&As [click here]
So—ready to ditch the "all-or-nothing" mindset? The real question isn’t *if* smart growth works… but *how* your unique mix of people, tech, and values can make it thrive. 🔍 Let’s dig deeper…
In exploring the hidden culprits of manufacturing growth, one may wonder: is automation truly the panacea for all our problems? While some argue that ramping up technology adoption can streamline operations, others caution against overlooking human factors. For instance, production efficiency metrics like machine utilization often reveal bottlenecks that tech can't fix alone. And what about quality control? Defect rates can skyrocket if workforce skills aren't up to par—raising a critical question: Are we investing enough in employee training?
Supply chain reliability also deserves scrutiny; lead times and inventory turnover might suggest a smooth operation, yet suppliers’ performance can spell disaster. This raises another point of contention: Is reliance on just-in-time inventory creating an illusion of efficiency? If the latest trends continue, how should small manufacturers adapt their strategies to ensure sustainable growth without falling into the automation trap?
To embark on your journey towards smart growth as a small manufacturer, start by taking stock of where you currently stand. Assess key metrics like production cycle times and defect rates—this is your baseline. Once you've got that data, pinpoint 2–3 areas for improvement that can deliver solid returns, such as boosting inventory turnover or cutting down energy consumption.
Now comes the fun part: pilot testing! Select a small project to trial your strategies. Set clear goals—like reducing waste by 15% in just 90 days—and track those results closely. Remember, communication is key; establish biweekly check-ins with different departments to share insights and adjust plans as necessary.
As you integrate new technologies or training programs, do it in phases over about six months. This will make transitions smoother and give everyone time to adapt. And don’t forget the power of feedback loops! They’re essential for refining your approach.
💡 Quick tip: Keep setting SMART goals throughout this process. For instance, aim to cut machine downtime by 20% within Q3 through predictive maintenance training.
If any hiccups arise along the way, remember: challenges often lead to unexpected opportunities!